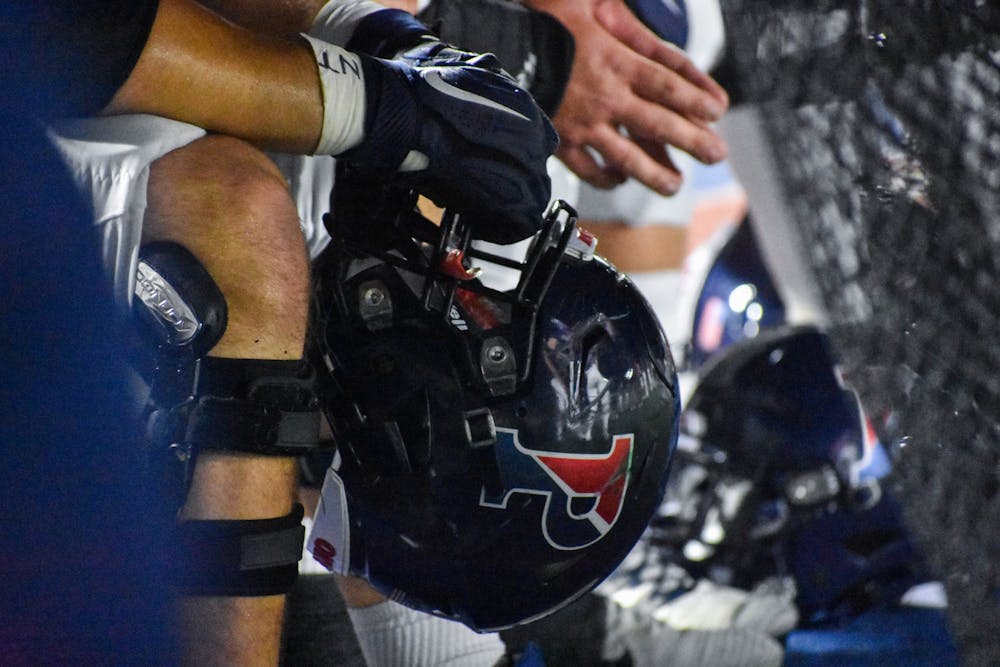
A Penn football player holds onto his helmet while at the sidelines during the team's game against Dartmouth at Franklin Field on Oct. 1, 2021.
Credit: Samantha TurnerThe cliche “look good, feel good, play good” couldn’t be more true when it comes to Penn Athletics and its equipment department.
Many people enjoy watching Penn's teams go out, compete, and look good in their uniforms. But few appreciate all the work that goes into making it happen behind the scenes. People like Matt Eagan, equipment operations manager of 18 different teams, Drew Flack, equipment manager of football and both lacrosse squads, and Cody Spence, equipment manager of nine different teams, do the work off the fields and courts to make the athletes look and feel better.
It looks like the Locust Walk design on the football and lacrosse teams' uniforms were a hit for many. Eagan said the inspiration for this design was something he’d been thinking about for roughly three or four years.
“[I wanted a way to] tie the campus and academics with athletes, as they can sometimes feel like separate things, to try to make them come together as one,” Eagan said.
Other sports like men’s basketball have key roots of the city like the Philadelphia skyline incorporated in their uniform designs. All the equipment managers say they pay attention to what's going on around them at the school, in the community, and even across other schools and professional leagues as well.
The gear and designs are planned out well in advance, with shipments and orders being placed as early as six to nine months before a team's season.
“Stuff like all of our shirts, shorts, and apparel was due a few weeks ago in October but won’t start shipping [until] around June and July,” Eagan said. “It’s a long, thought-out process requiring a lot of planning and thinking ahead."
“It's a year-round job that never really stops,” Spence added.
Many may think the role of an equipment manager is simply just to wash and order gear, but each of their everyday responsibilities goes well beyond just handling the team's laundry. The managers help set up for practice and game days, observe, and even run drills in certain instances.
Spence explains that he attends field hockey practices to watch how the athletes are responding to their new Nike turf shoes, to get feedback to Nike on what they like, and to collect any suggestions they might make to enhance the product for the benefit of the athlete. He says he is also very hands-on during game days with baseball, as he does the pregame bat-testing that is now required by the NCAA.
Flack, on the other hand, helps set up the practice field for football every day before the team hits the turf at the crack of dawn and is one of the last to leave as he then proceeds to clean it up as well, preparing for the next day even after all the players and coaches are long gone. He’s also actively engaged in football practice, he says, as he will help “spot the balls, snap the balls to the quarterback, hold the chains, and even run routes for the quarterbacks if need be.” Flack also drives an enterprise truck to each away football game with all the team's gear and equipment, sets up the players' lockers before games, and fixes lacrosse players' broken sticks.
The equipment team might not be on the field or court during the game, but their impact is felt all across the playing space, from the preparation to the uniforms.
The Daily Pennsylvanian is an independent, student-run newspaper. Please consider making a donation to support the coverage that shapes the University. Your generosity ensures a future of strong journalism at Penn.
Donate